Calik Denim Farm to Fabric Field Trip: Part 2
- Ani Wells, Anne Oudard
- Dec 18, 2023
- 5 min read
INTRODUCTION
Last week, we dove into part 1 of our field trip to Turkey with BCI and Calik Cotton meeting with farmers and visiting ginning facilities. As our cotton is now baled and labeled, we’re traveling north to Malatya from Sanliurfa to explore the spinning, dyeing and weaving at Calik Denim mill. Come with us as we embark on the 2nd and final part of our farm to fabric traceability expedition.
A JOURNEY THROUGH THE MILL
Yarn Spinning: A Visual Exploration
The next and last stop on our farm to fabric journey took us to Calik Denim mill, where all of that cotton gets transformed into fabric.
As we noted, traceability data is often stopped at the gin, stopping us from finding farm level data. But prior to this lies another hot spot where traceability gets tricky: blending cotton for spinning. To learn more, read Step 3 of our #WhoMadeMyCotton research study
Once the cotton was brought to the mill, we saw it being opened, cleaned and blended before it was spun into yarn. To keep track of the different cotton bales that are being blended to create a uniform yarn, Calik Denim uses physical tracer and blockchain technology through the tech provider AWARE for real time traceability taking us through the entire denim journey. The spun yarn is meticulously wound onto bobbins, each weighing in at around 3 kilograms, then sent to a steam treatment to relax the fibers and ditch the static, prepping it for its transformation into fabric.

Traceability Fun Fact: We saw a wall of coloured bobbins and outside of the eye catching image we all took, we wondered if color coding was also a means for traceability. We were pleasantly surprised to hear that it in fact was and not just for show. These colour coded bobbins allow workers to swiftly identify different fiber types and specific batches, helping to also increase efficiency. For example, a blue bobbin may denote organic cotton while red could be a man made cellulosic or branded fiber. The color-coding system is also really handy for quality control. When you shine a black light on the yarn, any imperfections stand out immediately and the colored bobbins make it easy to trace the yarn back to its source, ensuring that any issues are addressed quickly.
Dyeing: Transforming Cotton into Colorful Yarn
Next up on our denim journey: it's time to add some color!
We strolled over from the spinning unit to the dye range, just a few minutes away. Here, those bobbins we just watched being spun are getting ready to become "warp beams." These beams hold the yarn from multiple bobbins that will be dyed with indigo and/or sulfur for different denim shades.
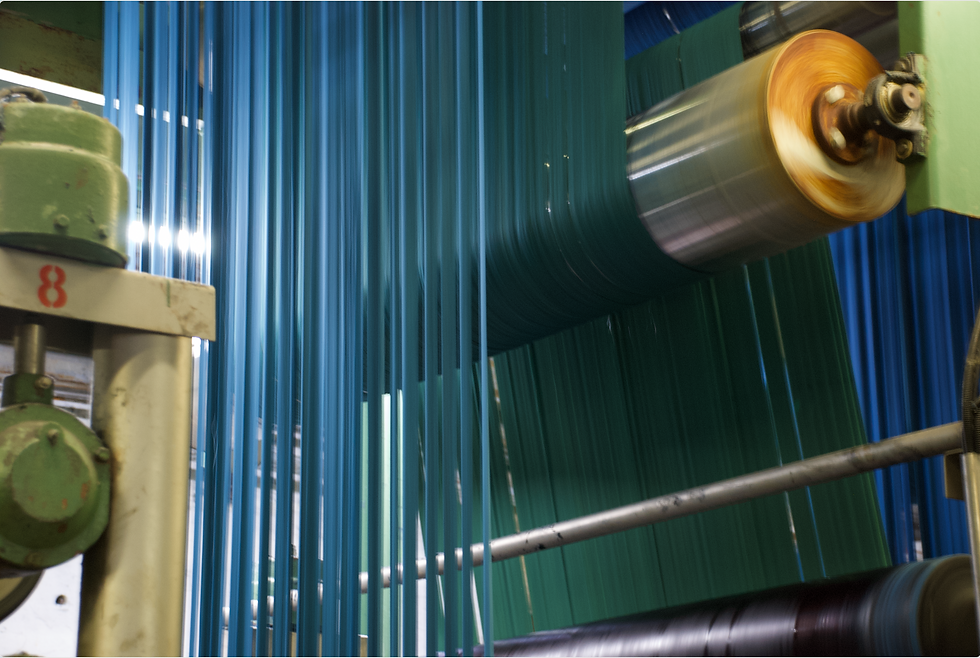
Because indigo is a living colour, the dye range is being monitored and sampled constantly to inform the technicians if anything needs to be adjusted, such as the pH level.
Unique to Calik Denim is their Dyepro technology that results in zero waste water, but what also caught our attention was the fact that the dyestuff and process is also traceable using the AWARE technology!
After the yarns have been dipped and oxidized, the yarns are prepped for weaving by adding starch and in Calik’s case, they use corn for its natural starch.
Weaving Highlights: Crafting the Fabric
Weave finally reached the stage where these fibers turn into fabric (excuse the pun). Moving over to Calik Denim’s weaving unit, we were introduced to an orchestra of looms playing in harmony. Here we saw yarn by yarn meticulously separated from the warp beams on the looms that had just been dyed, and woven together with undyed weft yarns to create yards and yards of denim fabric. Ta da!

But, that isn’t the end quite yet. After the fabric is woven it needs some finishing touches before it can go to cut and sew.
Finishing Highlights: Adding the Final Touches
From the weaving unit, we entered the finishing room. We first approached the singeing machine quite excitedly as we saw flames on the inside glowing. In this step, the woven fabric is sent through to burn off any stray fibers, giving it that smooth finish. Next, it might be washed, treated with certain chemicals, or have any sizing removed to get the desired hand feel. Next, the fabric's shrinkage is taken care of and its skew is fine-tuned by being fed between large hot rollers. Finally, it undergoes a sanforizing process, ensuring it's pre-shrunk and ready to maintain its shape.
The Digital Warehouse: Where the Traceability Journey Ends
Moving on to Quality Control and Stocking, the fabric, having undergone the sanforizing process, is ready for a thorough quality check. Once it gets the nod of approval, no human hands touch the fabric again! It's rolled up and stored with precision, tagged with an RFID for easy tracking, and just to give you a sense of the scale, this facility has millions of meters of fabric on standby, ready to be transformed into jeans bringing us to the end of our farm to fabric journey :)
BEYOND FABRIC: CALIK'S ROLE IN SPINNING AND SELLING YARN
Calik Denim doesn't only make fabric; they're also in the business of creating and distributing yarn. Having their own gin and vertical operations puts Calik in a unique position to take raw cotton, spin it into yarn, and then ship it off to other companies. These companies trust Calik not just for their quality but also for their ability to track the yarn's origins – it's all about knowing where and how things are made. Calik's yarn-selling game is about connecting the dots from field to factory, making sure every thread tells a story of quality and care.
CONCLUSION
Reflecting on the entire trip with Calik Cotton, Calik Denim and BCI, we feel as though we reached another level of education. Being able to follow the entire denim making process was a unique experience that not many in the industry do. We are extremely grateful for opportunities like this as it gives you the opportunity to connect with supply chain partners face to face, cultivating deeper relationships, as well as a deeper understanding of the local realities and regional contexts. The fact that Calik Denim organized this type of trip reveals a lot about the growing interest of the industry around farm level traceability. Every time you visit a field or a factory, you learn something new. That’s why we encourage anyone who has the opportunity to join one of these events to meet with the farmers, ginners and weavers in their supply chain!
Thanks again to Calik Denim for supporting this trip and stay tuned for Part 4 of #WhoMadeMyCotton launching next year.
Comentarios